The most common types of plastic parts are produced by thermoplastic injection molding. The term itself is suggestive, described briefly as the injection of liquid resin into a tool or mold to form plastic parts. There are two very different methods used to produce injection molded parts: 1) Cold runner system and 2) Hot runner system.
Years ago it was not uncommon to buy model car kits. The car parts connected to runners. This image depicts the cold runner process as the runners are a part of the product.
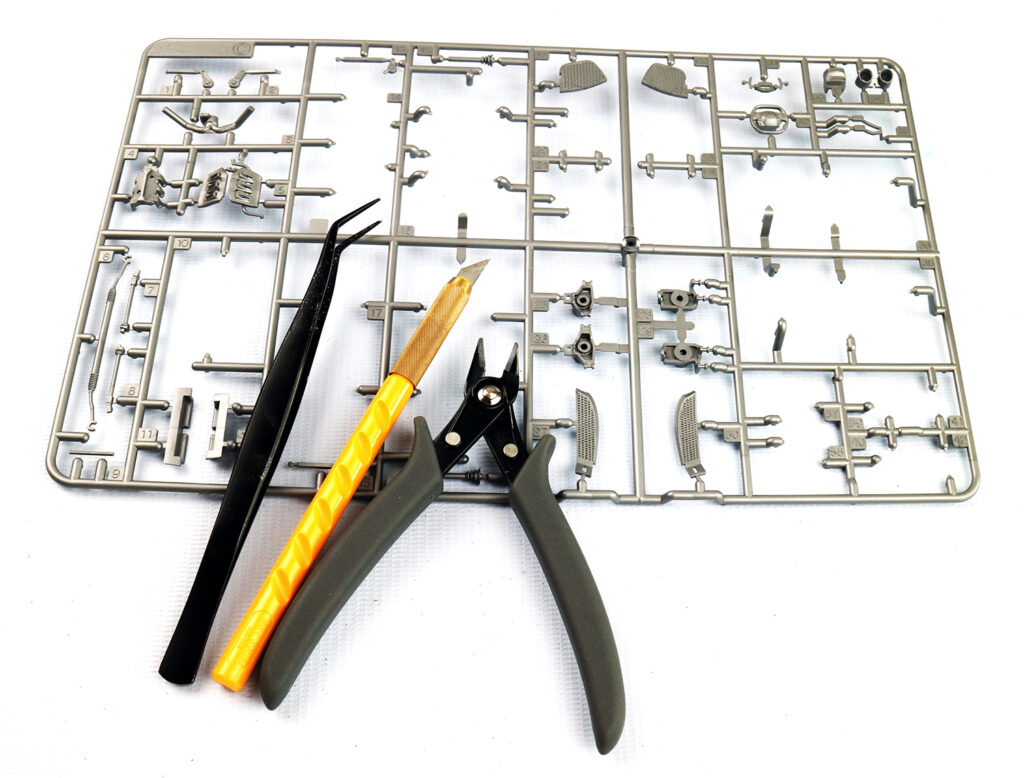
Cold and Hot Runner Systems
Cold Runner
- Scrap (runners or sprue)
- Less costly molds
- Higher per part cost
- Typically used for smaller volumes / low cavitation molds
- Hot liquid enters unheated channels.
- The liquid flows into the cool mold cavities through these unheated channels, which are the runners.
- The liquid solidifies throughout, including within the runners.
- When ejected the runners will need to be separated from the product. (scrap or waste)
- Filling and cooling time lowers production efficiency.
Hot Runner
- No scrap
- More costly molds
- Lower per part cost
- Typically used for large volumes / high cavitation molds
- The heated material maintains a molten state throughout the runner.
- The molten material flows into the cavity through the gate.
- The cavity forms the product, cooling while the runner remains heated, producing no sprue or scrap.
- Good thermal conductivity (fast heating, fast cooling) yields production efficiencies.
Knowing which system is best for your product is key. Working with our design engineers we assist in guiding the decision as to the options best suited for your requirements. Prior to actual production product design is given great attention by our engineers. Reviewing specifications to determine the best manufacturing process that will deliver the most cost effective result at the highest level of performance is certainly key. Matching production needs with the process requires a look at design, and once settled the next consideration is a mold.
A Concept for Thermoplastic Injection Molding
After the product design is established on paper, it is typical to create a prototype mold for testing. Prototype molds are made with much less expensive materials, intended primarily for temporary use to produce a small amount of product for testing approval. Once product produced using the prototype is approved a final production mold is created capable of enduring many hours, typically years of use.

Steel or aluminum are typical choices to produce a mold. Steel molds tend to have a longer lifespan but cost more than aluminum. If a customer plans to continue producing the part over a long lifespan, engineers will advise towards the steel mold option.
Also factoring into the cost of the mold is the number of cavities, which determines the full size of the mold and molding machine. Machines are different in many ways including minimum and maximum size molds each machine is capable of handling. Our engineers take this into consideration during the design stage.
A mold is two pieces, two halves of a whole (sometimes called mold plates). Each half will consist of one or more cavities. Each mold half is attached to a platen, a catalyst for controlling the movement of the molds. Platens move vertically or horizontally, and this depends on the machine design. (Read more on vertical & horizontal machines.)
The production process begins with solid plastic pellets fed into a hopper and passed through a heating device that can reach temperatures over 400°F, melting the pellets into a liquid resin. Preset automation or manual operations trigger the platens to close, drawing the mold halves together. The hot thermoplastic resin is injected into the closed mold at very high pressure. The point of entry to the cavity is referred to as the gate.
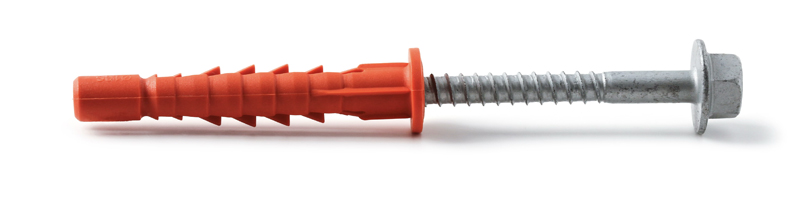
As the liquid is forced past the machine nozzle, it travels through the sprue, runner system and gates into the cavities. The mold itself is constantly cooled, and the heated material adheres to the cavity walls. The liquid resin cools down, solidifying into the shape of the mold, forming the part. The machine opens, the two halves of the mold separate, exposing the new finished part on one half of the mold. Ejector pins are activated to eject the solid part(s) from the mold half. Applying robotics increases the efficiency by removing the runners and/or parts.
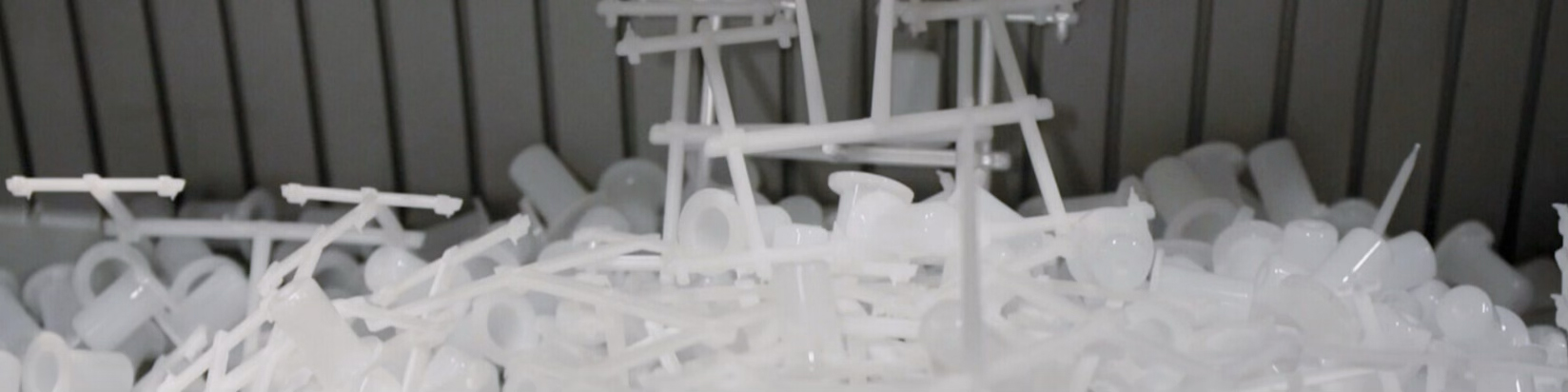
Materials
The most common materials used in injection molding processes are thermoplastics. The type of material factors in overall production. Material properties must be considered when the end part requires any specific quality or qualities. Of the many materials used in injection molding parts, GripWorks has processed all of the most common. Our capabilities include the use of engineered and commodity resins, as well as thermo plastic elastomers.
Material Qualities
Materials
Our production capabilities for injection molding in our USA and Southeast Asia facilities are wholly owned and operated.